Customer Support
Superior support from industry experts
At Garlock, we deliver customer support at a level that is unmatched by other packaging converters. Our team is responsive, knowledgeable, and committed to solving challenges quickly to keep your operations running smoothly.
With Garlock, you get more than packaging. You get a team that works alongside you every step of the way.
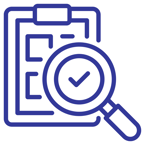
On-Site Packaging Audits
At your request, Garlock's technical team will visit your facility to perform a full packaging audit from material receipt and storage to how it runs on your equipment.
You'll receive a detailed report with actionable insights to boost performance, reduce costs, and improve efficiency all at no cost. We believe these audits are a key part of our responsibility to ensure every aspect of our customer's packaging processes are as lean and efficient as possible
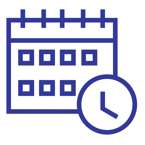
Shelf-Life Testing
Garlock offers expert shelf-life testing to help you optimize packaging for your product's specific needs. Whether you're aiming for a 3-month or 12-month shelf-life, our team evaluates your current materials and recommends cost-effective alternatives to meet your goals. We also offer MAP testing to detect leaks and protect product integrity.
With over three decades of experience and proven modeling, Garlock helps ensure your packaging performs efficiently and reliably.
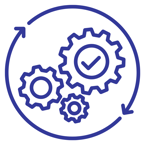
Machine-Material Interactions
Garlock ensures your packaging materials are fully compatible with your equipment whether it's a vertical or horizontal machine, flow wrapper, or a fill-seal unit. During in-field trials, our team provides hands-on support to test materials, optimize settings, and ensure peak performance at full production speed.
From first trial to full scale-up, we're by your side to keep your packaging running efficiently and help you reach the market faster with confidence.
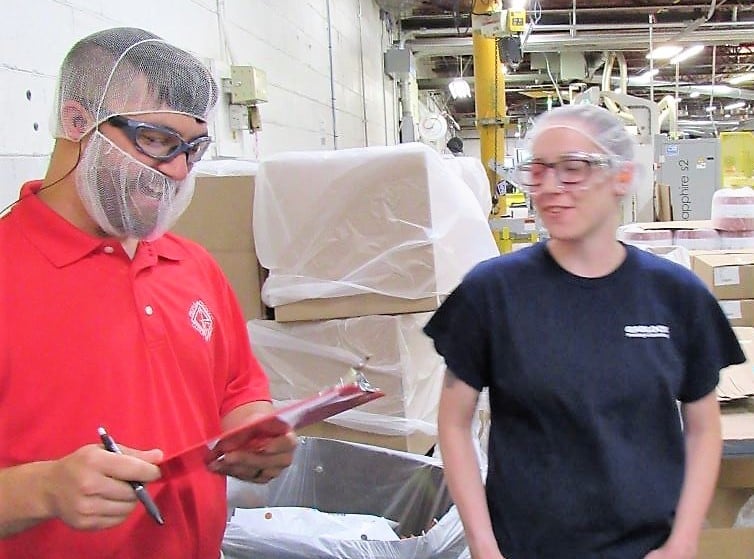
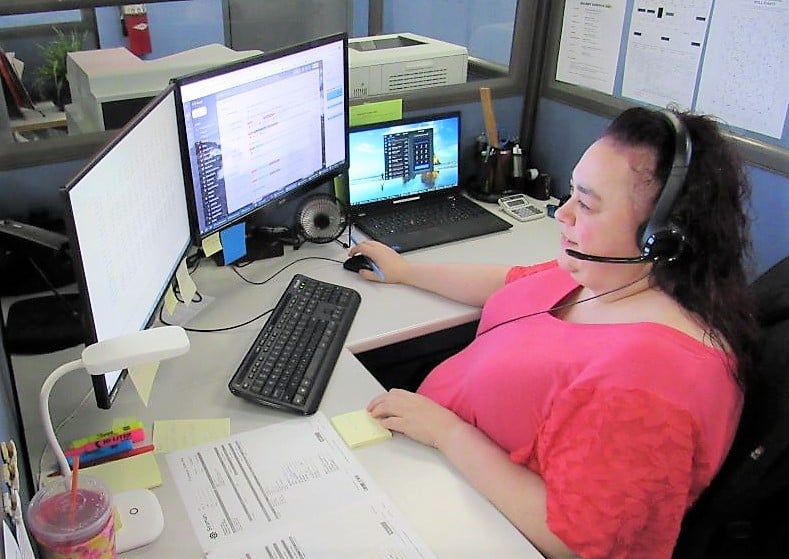
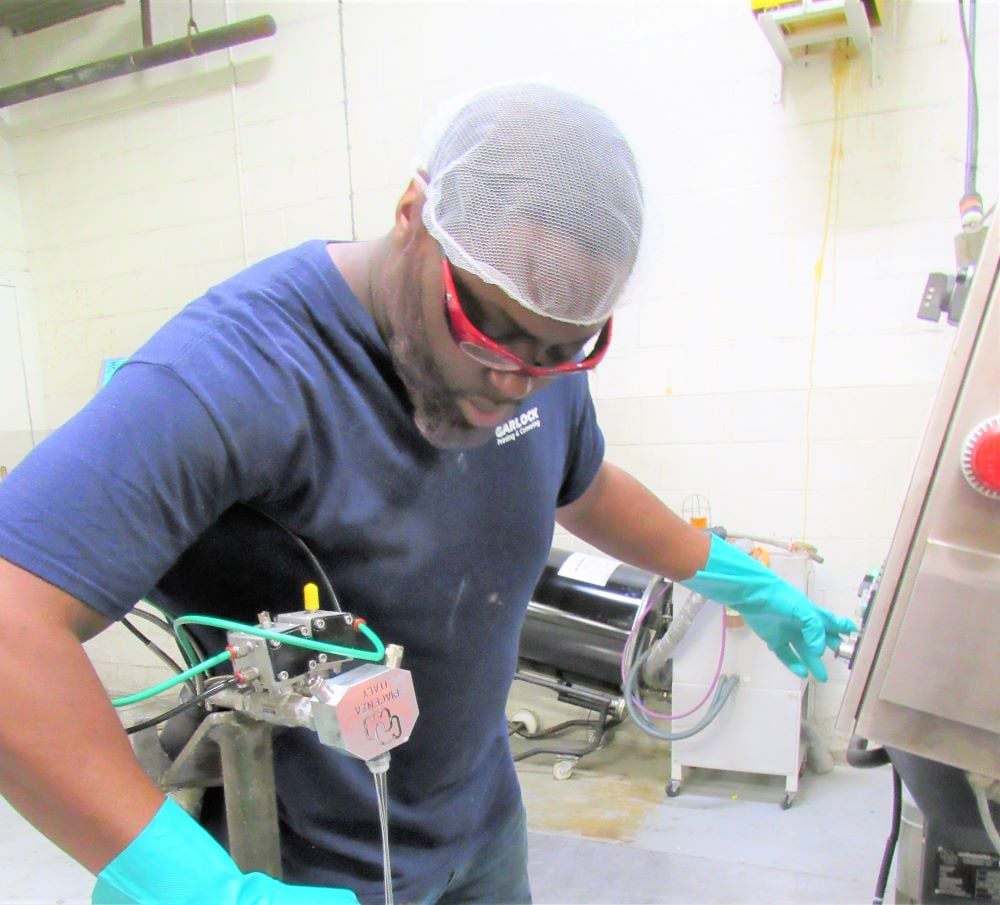
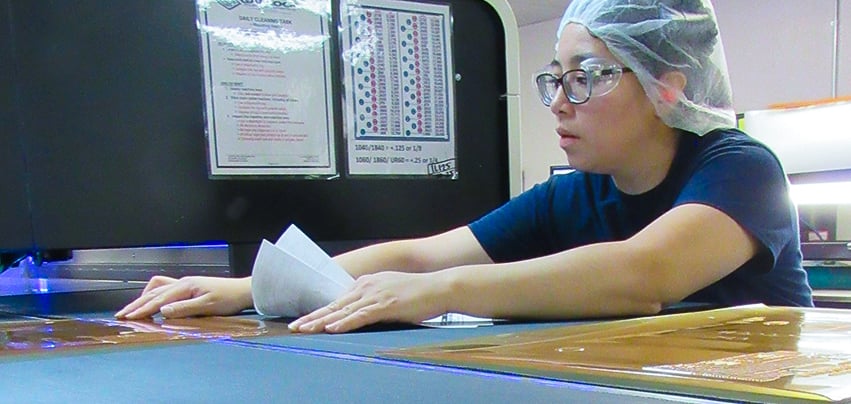